12 Frequently Asked Questions about heat flux
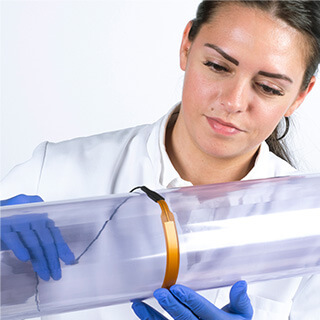
curved surface with the FHF05-15X85
heat flux sensor.
This article answers the most frequently asked questions concerning heat flux and heat flux sensors. From basic definitions to their practical applications and measurement techniques. Whether you are a student, engineer, or simply curious about the thermal dynamics of your environment, these FAQs offer a good introduction to the field of heat flux measurement.
1. What is heat flux?
Heat flux refers to the rate at which heat energy passes through a surface per unit area measured in W/m2. It is a vector quantity, meaning it has both magnitude and direction. Its measurement is crucial in processes like thermal management, energy conversion, and material science. Furthermore, it dictates how we manage heat in systems and indicates the energy efficiency of processes in our daily lives and industrial settings.
Heat flux is measured in several fields and industries. For example, engineers must account for heat flux when designing electronic devices to prevent overheating. In buildings, these measurements help to improve insulation and, thus, energy efficiency. Environmental scientists study the climate by measuring heat flux in the earth’s surface.
Read more in our article: What is heat flux?
2. What causes heat to flow?
Heat flux occurs because of temperature differences. The second law of thermodynamics states that heat will always flow from higher to lower temperatures. This heat flow will continue until the system or object reaches thermal equilibrium.
The factors that affect the magnitude of heat flux include:
• Thermal conductivity and specific heat of the material.
• The temperature difference between environments.
• The mechanisms by which heat is transferred.
For example, when subjected to the same temperature differences on either side, an excellently insulated thick wall will have a lower heat flux than a thin glass window.
3. How is heat flux measured?
Heat flux sensors measure the amount of heat energy passing through a surface and typically also measure temperature. Users place these sensors in the path where heat transfer is present- between the heat source and sink- to capture the energy exchange. When heat passes through, the sensor measures watts per square meter [W/m2]. These sensors can be in the form of a thin, delicate film or as a sensor with robust housing.
Heat flux measurements not only indicate the intensity of heat, but also the direction. This is crucial for optimising thermal designs.
Measuring heat flux requires careful calibration of sensors and an understanding of environmental factors. The sensor placement is also critical. The placement must represent the overall heat transfer and not be subject to localised effects.
Read more in our article: How to measure heat flux?
4. How is heat flux calculated?
Heat flux is the amount of energy passing through a unit area per unit time. You can estimate heat flux using different formulas depending on the mode of heat transfer. Heat can be transferred through conduction, convection, and radiation.
For conduction, thermal energy transfer takes place within a body or between two bodies in direct contact (most often in a solid). The formula for one-dimensional heat conduction is:
With:
- q the heat flux (W/m2)
the thermal conductivity of the materials (W/mK)
the temperature difference across the material (K)
the thickness of the material (m)
The negative sign indicates that heat flows from high to low temperatures.
For convection, heat is transferred by moving fluids, which can be liquid or gas. The formula for convection is:
With:
- q the heat flux in (W/m2)
the convective heat transfer coefficient (W/m2K)
the surface temperature (K)
the fluid temperature (K)
For radiation, heat is transferred in the form of electromagnetic waves or photons. Unlike conduction and convection, radiation does not require matter to transfer heat. The rate at which a body with a given temperature emits thermal radiation is provided by:
With:
- q the heat flux in (W/m2)
the emissivity of the surface material
the Stefan-Boltzmann constant (5.67 * 10-8 W/m2K4)
the absolute temperature of the surface material (K)
the absolute temperature of the surroundings (K)
Note that these formulas work for one-dimensional and steady-state conditions. In multi-dimensional and transient conditions, calculations require solving partial differential equations.
5. What is the difference between heat flux and heat flow?
People often confuse heat flow with heat flux. They are both related quantities in thermodynamics but have distinct meanings. As mentioned above, heat flux is the rate of heat transfer per unit area measured in watts per square meter (W/m2). It has both magnitude and direction. It is a local measurement that measures how much energy passes through a specific area. Sometimes, it is also called heat flow density because of the measurement through a surface.
Heat flow, however, refers to the total amount of transferred heat measured in watts [W]. It is a scalar quantity, meaning it only measures the magnitude of energy transferred. Heat flow indicates how much heat transfers through the entire surface area per second. For example, if you’re heating a building, the heat flow would be the total energy entering and exiting the building per second.
So, heat flux is about intensity and direction, while heat flow is about total. Both per time unit. Both are important for understanding systems involving heat transfer but serve different purposes.
6. What is the difference between heat flux and temperature?
Heat flux and temperature are related but have different qualities in thermal physics. Heat flux is the rate heat energy transfers through a unit area per second. It tells you how much energy is transferred per unit time and in which direction it moves.
In comparison, the temperature can exist without the movement of heat -for example, a uniformly heated room. Temperature relates to the average kinetic energy of particles. The higher the kinetic energy of particles, the higher the temperature. It does not indicate how energy is moving or changing within a system.
7. What is a heat flux sensor?
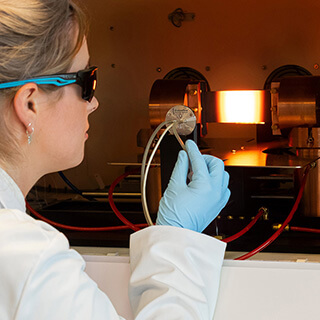
the GG01 Gardon gauge
water-cooled heat flux sensor.
A heat flux sensor is an instrument that converts thermal energy passing through it into an electrical signal. Its output has a known dependence on how much heat energy transfers through a surface per unit time. In many fields, these sensors are used, such as building insulation testing, environmental monitoring, and process control in manufacturing. They can also help characterise materials and ensure systems operate within thermal limits.
These sensors come in various designs tailored for specific applications and environments. They typically consist of a thermopile to measure heat flux and a thermocouple to measure temperature.
Different types of sensors:
- Gardon gauge (For test reaction to fire and fire resistance testing. Environment dominated by radiation)
- Schmidt-Boelter (For test reaction to fire and fire resistance testing. Environment dominated by radiation)
- Flare radiation (For alarm systems. Environment dominated by radiation outdoors)
- Thin foil film (Often flexible for varied surface types and diverse environments)
- Flux plate (Rigid, for soil, walls, building envelopes, …)
Each type of sensor has its range of applications, accuracy levels, and operational limits. The choice of the sensor depends on the specific requirements of the measurement task. Take a look at all heat flux sensors.
For more information on the types of sensors and their latest technologies, please read the article: Heat flux sensors: the latest technologies.
8. How does a heat flux sensor work?
A heat flux sensor measures the temperature difference across the known thermal resistance of the sensor. There are different types of sensors specifically constructed for various applications. Therefore, how they work and how they are installed can differ. Here is a simple conceptual step-by-step explanation of the working process:
- Thermal contact: You place the sensor in thermal contact with the surface or medium where heat changes.
- Heat absorption: On one side, the sensor absorbs heat, which is transferred across the sensor’s body to the other side.
- Temperature gradient: This transfer happens because of a temperature difference or temperature gradient around the sensor.
- Electrical signal: The thermopile within the sensor generates an electrical signal proportional to this temperature gradient.
- Data: The electrical signal is then interpreted by a data acquisition system, which uses the known properties of the sensor. Here, the actual heat flux is calculated using the sensor's sensitivity.
Understand that there are various heat flux sensors and that this is a general explanation of how these sensors work.
9. What are the limitations of heat flux sensors?
There are various heat flux sensors built specifically for different applications. Therefore, these sensors have diverse specifications and rated working ranges. Some limitations that you must consider are:
- Temperature range: Each sensor is designed to work in a specific temperature range. If you exceed the rated range, you can damage the sensor, leading to inaccurate readings.
- Response time: Some sensors may take more time to capture rapid changes in heat flux. You will need a fast response time sensor in an environment with rapid heat transfer rates. If the sensor’s response time is slower than the changing heat flux, you cannot measure it accurately.
- Sensitivity: The sensitivity of a sensor determines the ability to detect more minor changes in heat fluctuations. High-sensitive sensors will detect smaller changes.
- Calibration: Sensors must be calibrated for accurate measurements. The sensor can be affected by environmental conditions and must be regularly checked.
- Surface contact: Ensure your sensor has good thermal contact with the surface for accurate measurements.
- Measurement range: Besides the temperature range, the sensors also have a heat flux range. Measuring outside this range can worsen the accuracy.
It is important to know that no single sensor is suitable for all applications. Choosing the right sensor requires a good understanding of the application and the sensor’s characteristics. If you are unsure about which sensor to choose, Hukseflux can assist you in determining the best one for your needs. Do not hesitate to reach out to us for further assistance.
10. How are heat flux sensors calibrated?
Calibration is an essential process that ensures the accuracy and reliability of the measurement. Calibration means you compare the sensor’s output to a known reference under controlled conditions. Here is an overview of the calibration process:
- Reference standard: To calibrate the sensor, you need to have a reference heat flux source of known value.
- Controlled environment: The calibration must happen in a controlled environment. Here, you must be able to control the temperature, humidity, and other factors. This will prevent measurement errors.
- Mounted sensor: The sensors must be mounted correctly to ensure good thermal contact.
- Applying known heat flux: Now, apply the known heat flux to the sensor. This can be in the form of radiant or conductive heat sources.
- Output: The sensor’s electrical output is now measured using the known heat.
- Sensitivity: You can determine the sensitivity by comparing the electrical output to the known heat flux. This factor will convert future measurements into actual heat flux values.
- Repetition: Repeat the process to check consistent results.
- Documentation: Record all data for traceability and future reference
- Certification: If a calibration service performs the calibration, a certificate is usually issued detailing the performance and calibration factor after successful calibration.
Table 1 shows Hukseflux’ calibration services for heat flux sensors with the corresponding calibration method.
Table 1: Hukseflux heat flux sensor calibration services.
HUKSEFLUX CALIBRATION SERVICES | |||
Calibration item | Brand and model | Calibration method | Comment |
Heat flux sensors (high flux) | Hukseflux:
| ISO 14934 Fire tests - Calibration and the use of heat flux meters - Part 3: Secondary calibration method. Transfer calibration by comparison to a secondary standard under a radiant source. Calibration may be performed at multiple flux levels, also for one sensor. Calibration up to 100 x 103 W/m2 | Concerning heat flux sensors, Hukseflux is not an ISO / IEC 17025 accredited laboratory; users may need calibration of their local reference measurement standard at an accredited laboratory for certified fire testing such as Rise, NIST or LNE. Hukseflux’ calibration reference standard is calibrated up to 75 x 103 W/m2 |
Heat flux sensors (low flux) | Hukseflux: HFP series FHF series | Hukseflux internal method HFPC. This method is validated against ASTM C1130 Standard Practice for Calibrating Thin Heat Flux Transducers |
Some sensors come with a self-calibration model, like our FHF05SC series. Otherwise, you need to send your sensors to a calibration service.
11. When do you have to calibrate a heat flux sensor?
The recommended calibration period is suggested in the manual. Calibration is necessary for accurate measurements. Therefore, we recommend calibrating your sensor once a year, but this is not obligatory.
Standards like ISO 9001 recommend regular calibration by an accredited laboratory at intervals not exceeding two years. If you exceed this interval, your ISO 9001 certificate will not be valid.
12. How do you use a data logger?
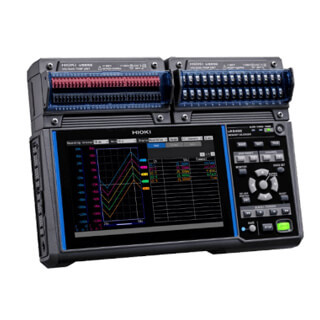
plug-in modules installed. The logger can connect
to wireless units and can handle 165 heat flux
sensors each with its own temperature
measurement.
Data loggers are electronic devices that automatically monitor and record data. Below, you can read a step-by-step guide for using the Hukseflux FHF05 series or FHF06 heat flux sensors with the Hioki LR8450-01 data logger. This serves just as an example; in fact, you can connect Hukseflux heat flux sensors to most data loggers.
- Select the right data logger and sensor type for your specific application. For example, when measuring temperature and heat flux from building envelopes. You can connect Hukseflux’ FHF sensors to the Hioki LR8550-01 data logger.
- Install the sensor correctly. For instance, in building insulation studies, the sensor is placed between layers of material. Mount the sensor securely to minimise air gaps or thermal resistance.
- Connect the sensor to the data logger. Sensors are connected to the data logger via cables. Suggested wire connection of FHF05 series or FHF06:
• Ch 1 +: red (heat flux +)
• Ch 1 -: black (heat flux -)
• Ch 2 +: thermocouple (type T +)
• Ch 2 -: thermocouple (type T -) - Specify measurement. This might include measurement range, maximum heat flux, data logging interval, etc. For the Hioki and FHF combination, you must do the following steps:
• estimate the maximum heat flux
• calculate the output range of the heat flux sensor in [× 10-6 V] and program it into the logger; sensitivity x maximum flux
• for Ch 1, choose as input ‘voltage’ and program the sensor's sensitivity as the scaling factor for heat flux measurements.
• for Ch 2, select as input ‘Tc’ and then Type T
for temperature measurements. - Start measurement. Press the start button. The screen will display heat flux and temperature simultaneously.
- Store data using a USB flash drive, SD card or connection to a computer.
If you have more questions, please contact us.