Measuring heat flux in industrial environments
This article is about heat flux sensors used in industrial processes: industrial heat flux sensors for high temperatures, and also industrial heat flux sensors for high heat fluxes such as Gardon gauges and flare radiation monitors.
It starts with explaining what the different requirements are for industrial use. Then, it lists the sensors Hukseflux offers. For each sensor, there is a short explanation of its working principle, their different applications and when to use it.
What are the requirements for measuring heat flux?
In industrial environments, the temperatures and heat fluxes can reach high values. To survive these extreme conditions, the sensors have to be robust. The sensors at Hukseflux are designed to be durable in these high temperatures (-150 °C to +900 °C), water, outdoor… If it is relevant, the sensors follow industrial standards such as ITS90, ANSI, DIN, and BS.
How does a heat flux sensor work?
All the sensors mentioned below measure the heat flux through itself using a thermopile. The temperature difference in this thermopile creates a small voltage. This voltage can be measured using a voltmeter that works in the millivolt range. For more information on this principle, please read the article: How to measure heat flux?
Almost all sensors use a thermocouple type K to measure temperature besides the heat flux. This ensures a more accurate measurement. The HF02 flare radiation sensor uses a thermocouple type KX. The HF03-LI19 portable heat flux sensor is the only one that does not use this principle.
Which sensor is needed?
Which sensor is needed depends on the environment and what type of heat flux has to be measured. There are three types of heat fluxes: conduction, convection and radiation. Conduction is the heat flux through a solid material like a wall. Convection can be measured when the heat flux is transferred by a gas or fluid. Radiation is the energy that almost every object releases. The most known are light or heat from a fire.
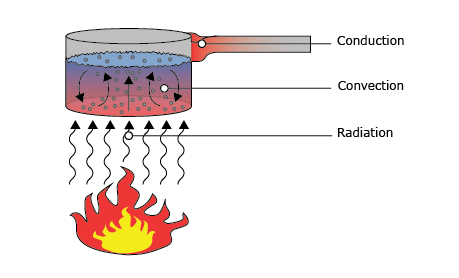
To measure radiative flux, a sensor must be equipped with an absorbing, usually black, coating. This coating absorbs the radiation and converts it to conductive heat. The conductive heat flux is then measured by the sensor. It is proportional to the incoming radiative heat flux.
The following list provides for every type of heat flux which sensors can be used.
- Radiation: flare and fire radiation sensors; Gardon gauge and Schmidt-Boelter gauge; IHF01, IHF02 and HF05 industrial heat flux sensors.
- Convection: HFS01; Gardon gauge (without sapphire window) and Schmidt-Boelter Gauge.
- Conduction: IHF01, IHF02 and HF05 industrial heat flux sensors.
Next is a list of the three types of sensors that can be used in industrial environments.
Flare and fire radiation sensor
The flare and fire radiation sensors can be used when the heat flux mainly consists of radiation. They all have a black, absorbing surface. Hukseflux offers the HF02 flare radiation monitor, the HF03-LI19 portable heat flux sensor with read-out unit and the HFS01 high heat flux sensor. The uses for these sensors vary. They are mostly used for flame monitoring: while outdoor, during fire-safety demonstrations, with high-intensity flames and during research.
The HF02 should be used in combination with temperature sensors and cameras. It is not recommended to use it as the main source of measurement. This is why this high heat flux sensor is mainly used in alarm systems. It alarms when the heat flux is above 5 x 10³ W/m² or when the sensor body is above a temperature of 70 °C.
The HF03-LI19 is used in fire testing. It can also be used to verify the performance of other flare radiation monitors. The measurements have to be short, because the portable sensor has a maximum exposure time of 10 minutes. For the LI19 to work, it is needed to enter the sensitivity. This sensitivity is provided on the product certificate of for example the HF03.
The HFS01 sensor measures, besides radiation, convective heat flux. It is also possible to order the sensor without black coating. This way, the absorption of radiation is reduced to measure the convective heat flux better. The sensor is water-cooled, usually by tap water.
The HFS01 sensor body can withstand temperatures up to 650 °C. This maximum temperature is limited to 240 °C when the low temperature extension cable is used. To increase the limit, use the high temperature extension cable.
While all three sensors measure flare and fire radiation, they have different specific uses. This is important to keep in mind while choosing the best sensor for your application.
Gardon gauge and Schmidt-Boelter gauge
The Gardon gauge (GG) and Schmidth-Boelter gauge (SBG) sensors are used in similar cases but use different technologies.
The Gardon gauge is made using a kind of copper which has a high thermal conductivity. Added to this, are thin foils made of a mix of copper and nickel. The radiation is converted to heat in the black coating. Afterwards, the heat flows through the foil to the sensor body.
There are two wires, one connected to the middle and the other connected to the outside of the foil. Between the two wires is a voltage difference, which is approximately proportional to the temperature difference. The water-cooling is essential because it keeps the sensor body colder than the foil. This technique only uses metals, which helps the sensor withstand extremely high temperatures.
Hukseflux offers the GG01 Gardon gauge sensor that uses this technology, which has 3 types. Each type has a different sensitivity, heat flux range and temperature range.
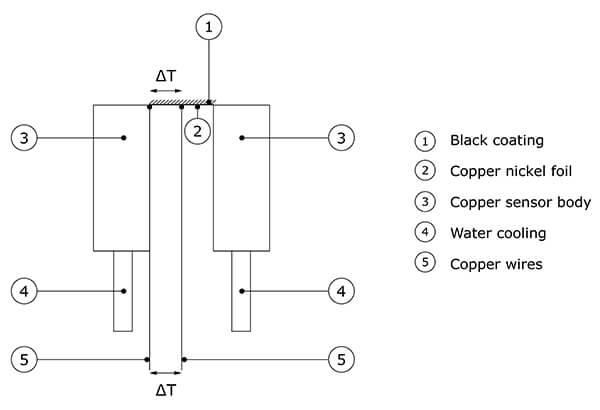
Next is the Schmidt-Boelter gauge senor. This sensor uses a combination of foil technology of the Gardon Gauge and thermopile technology of the Schmidt-Boelter Gauge. We offer two different SBG sensors: the SBG01 and SBG04.
The SBG01 is popular for fire testing. The high heat flux sensor also comes in 6 different types. The SBG04 is one of our newest products. It is mainly designed as a calibration reference standard for testing with cone calorimeters.
The heat flux that is measured by these three sensors is dominated by radiation, but it is an open sensor. This means that convective heat flux is also measured. The contribution of this heat flux is usually ignored. One of the types of the GG01, the GG01-250, can be equipped with a sapphire window. This window limits the measured heat flux to only radiation for a more exact measurement. The sapphire window picks up the heat flux via convection in the air and only passes the heat flux through the radiation. However, this accessory reduces the field of view from 180° to 150°.
The main use of these sensors is in situations with extremely high heat fluxes. To test for example flammability, fire resistance and reaction to fire. The sensors are also used in smoke chamber tests as a calibration reference standard.
The sensor of the GG01 can withstand really high temperatures, but the sensor body can only go up to 200°. The cable termination ends are the most vulnerable and have to be kept at a maximum of 105°. It is important to keep this in mind.
The GG01 has a wider range of both heat flux and temperature. Even though this maximum temperature is only for the sensor and copper housing. Other parts of the GG01 have lower maximum temperatures. For really high temperatures, this sensor is the best choice.
The SBG01 is useful for lower heat fluxes and also a lower temperature range. With a maximum of 200 °C for the cable, the sensor body itself can only reach 80 °C.
SBG04 has the lowest range compared to the best types of the other models. The sensor body itself can only reach a maximum temperature of 80 °C. However, this sensor can be used for specific uses like a calibration reference standard.
The reason these sensors can reach high temperatures, is because they are all water-cooled.
Industrial heat flux sensor
The industrial heat flux sensors IHF01, IHF02 and HF05 sensors are designed to measure extremely high heat fluxes, mostly conductive heat flux through a surface. The sensors can be used in trend monitoring and comparative measurements. They can measure an installation’s energy balances and the thermal transmission of walls. This is done by measuring heat flux and surface temperature in industrial installations.
If needed, these sensors can optionally be coated with black absorbing paint, to also measure the radiative flux.
All three sensors are equipped with an IP67 rating. This means that they are able to withstand extreme conditions like water and high pressures.
The IHF02 can be installed using a magnet frame for easy mounting. This frame does decrease the temperature range from 900 °C to 500 °C. The operational temperature range of the IHF01 can decrease to 240 °C when the low temperature extension cable is used.
The IHF02 heat flux sensor has a high sensitivity while operating at high temperatures. The IHF01 has a lower sensitivity, but this results in a wider range. If there are no high temperatures present, the HF05 is a more economical option.
Conclusion
There are many possibilities when it comes to choosing a sensor to measure heat flux in an industrial environment. It is important to consider what heat flux you want to measure, estimate the heat flux range and the temperature of your environment. Do not hesitate to contact us at Hukseflux for more information or to help you in choosing the right sensor.