Heat flux sensors in industrial furnaces
In 2013 an article was published by ‘The Italian Association of Chemical Engineering’, or AIDIC. The article, written by J. Vondál and J. Hájek, is titled: ‘Heat Flux Measurement Methods for Process Furnaces – a Case Study’. The heat loads on heat exchanging surfaces are important to monitor considering the efficiency, safety and lifetime of industrial process furnaces. This paper provides a comparison of two different models to measure the heat flux distributions inside a furnace, giving insights to both researchers and industries.
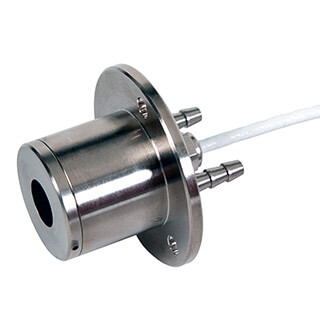
Heat flux measuring methods
This study compares two methods of heat flux measurement in a laboratory combustion facility. The first method uses a water-cooled Schmidt-Boelter sensor, the Hukseflux SBG01 heat flux sensor, commonly used in industrial practice. This is considered the standard method. The second method utilizes a segmental design and measures the total heat flux on the cooling medium of the furnace, in this case water. The paper provides a comparison of the heat flux distributions measured by both methods and analyzes their strengths and weaknesses.
Setup of heat flux measuring experiment
The experimental setup involved a cylindrical combustion chamber with water-cooled walls and insulated end walls. The chamber had a segmental design allowing for heat flux measurement in each segment. The experiment used a novel segmental measurement method, measuring the heat flux by analyzing the heat balance on the cooling medium in each segment. The object of measurement was a 745 kW non-premixed, swirl-stabilized flame of natural gas with air.
Why measure heat flux?
The measurement of heat flux is essential for analyzing combustion system performance. It is used to monitor fouling on heat exchange surfaces and to understand heat flux distribution on combustion chamber walls. Heat flux measurements are also used to validate computational fluid dynamics (CFD) combustor models. Read more about heat flux measurements in our article: How to measure heat flux.
Conclusion
The new, segmental method proved to be very accurate, providing values that directly correspond with heat fluxes occurring in real fired heaters. Comparing this to the standard method, using the Hukseflux SBG01, there was a drawback for the new method. The experimental facility required a steady-state operation for at least 50 minutes to obtain reliable data. This makes the new method not very easy to use.
Most existing methods for measuring heat flux through furnace walls do not capture the true heat flux value due to sensor limitations and the harsh environment. With this in mind, the writers of the article are convinced that this new method should be further examined.
Learn more about the different applications of the Hukseflux SBG01 heat flux sensor.
Original article: “Heat Flux Measurement Methods for Process Furnaces – a Case Study”.