In 2020 Hussein Humaish wrote an article titled: “Evaluating a line heat source method using a COMSOL Multiphysics axisymmetric 2D model”, which was then published by ‘IOP Publishing’. This study was conducted to find out if the TP02 Hukseflux thermal properties sensor is suitable for measuring the thermal conductivity of insulation materials, and if so, to see if this probe could be modelled correctly in COMSOL to do further experiments.
In this article the importance of thermal insulation in buildings is discussed to reduce energy consumption and greenhouse gas emissions. The lack of studies on the aging of insulation materials is also part of the motivation for this study.
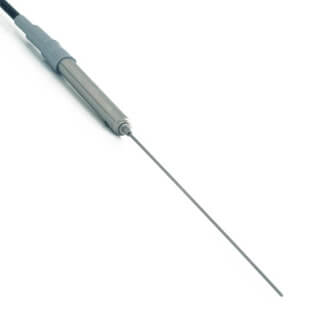
Modelling the TP02 thermal properties sensor
The TP02 non-steady state probe by Hukseflux was used to measure the thermal conductivity of glass wool, an insulation material. Calibration of the probe was done using glycerol, because of its lack of porosity and contact resistance. Also, the temperature variation across the logarithm of time is linear for this material, making it a reliable reference. Then, a model of the probe was made in COMSOL Multiphysics to see whether the experimental measurements complied with the theoretical values. To model the probe correctly, the contact resistance had to be accounted for. The model showed that, for using glass wool, the contact resistance should be modeled to represent an air gap of 1 mm.
The thermal conductivity measurements of the TP02 Hukseflux probe proved to be in line with the previously known values for glycerol (0.29 W/mK) and glass wool (0.04 W/mK).
Further theoretical experiments
With the correctly modelled COMSOL probe, it was then possible to perform simulations that could not be done with the actual probe. Two parameters of the probe were adjusted to look at the effects of the modelled thermal conductivity.
The outer layer of the probe is made from stainless steel. In the simulation, it was made clear that changing the thickness of this layer effects the measured thermal conductivity. Changing the layer from 0.33 mm to 1.00 mm changed the measured thermal conductivity of glass wool from 0.034 W/mK to 0.068 W/mK. The article suggests using nickel or copper instead of stainless steel to reduce the variation in thermal conductivity.
Secondly, different length/diameter ratios, or L/D-ratios, of the probe were modelled in COMSOL. The model showed that different L/D-ratios result in different measured thermal conductivities. Especially L/D-ratios below 75 created very different results in COMSOL. Logically, the shorter the probe, the more heat flows through the top-surface of the probe relative to the side of the probe. The heat flowing through the top-surface of the probe is neglected in the calculation of the thermal conductivity.
Because the Hukseflux TP02 needle probe has an L/D-ratio of 100, there is no risk of deviation in its measurements. The TP02 provided reliable measurements and the model in COMSOL proved to be accurate in comparison to the real experiment.
Original article: “Evaluating a line heat source method using a COMSOL Multiphysics axisymmetric 2D model.”